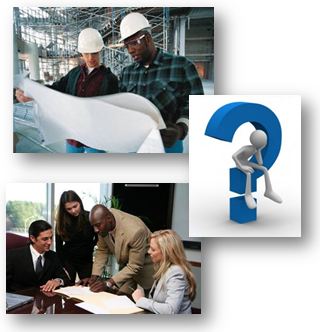
I was surprised, to say the least, that Corrective action system was being used to discipline employees (and thus, the CA’s issued to employees stored by HR in employee’s files together with the disciplinary notes- warnings). Also, I was told that my function will be to POLICE the quality and to make sure no bad products leave the plant.
In general, in my many years in different quality functions with various industries, the impression I had from other departments about quality folks is one that quality only knows about complaining, rejecting a lot, about issuing CARs etc. They don't seem to be proactive in sharing a problem but also in providing a solution. They are burden, not value added to the company.
If these people are expected to solve others' problems, the risk is that the QA person becomes responsible for the outcome in a process not in that person's control. QA people can advise but execution and decision-making is up to the process people. QA people can use the basic QA Management Tools to help facilitate the problem solving process and be coaches. These tools could sometimes be used in a meeting, and including representatives from various affected departments, where technically superior people and process owners/contributors can provide the input while the QA person asks the questions and uses the answers to execute the tools. Do this often enough and one could hope the process people can be steered toward adopting such tools for smaller level, day to day problem solving. The resulting solutions thus belong to the process (engineering) people, and the QA person is just facilitator.
As for the Police function, it requires Corrective Action to be elevated from the police action, and to focus on process (not on employee), and how it can be improved as to prevent the operator to miss again (training, error proofing, lean management, etc.).
In one instance I was doing internal audit, and I took a department's procedure, which was unclear on things like responsibilities. I made a bunch of notes on it that explained to the document's owner (department manager) what was needed. No need for him to guess and for us to push the thing back and forth until he got it right. Under old-style CA system, an auditor would be discouraged from teaching, but I feel it's a good time to move from cop to teacher (or coach). It's what my employer wants, which is especially important.
I wonder if your organization is sending mixed signals. Is the system set up through management for QA to behave in the Police Department mode and the process people are unhappy with the model? If so, the idea of coach/facilitator should be presented to management so everyone can understand the change QA is trying to make and why.
There will always be negative reaction to change. And if CA is issued to one department, its supervisor will always see it as a threat to his personal leadership and will go into defensive mode (“It’s not my fault”).
One way to accomplish the change of perception of the CA issued is developing a kindred relationship with a problem supervisor. Let him or her know that you aren't the cop, but just another guy fighting the same problem. Use Socratic questioning: instead of saying, "There's a problem and I'm here to solve it," which will almost always be perceived as threatening, use a series of conversational questions which will result in the supervisor coming up with the answer on his own. Start by suggesting that you're looking for help from him: "I have this problem x, and you have some experience in this regard, so maybe you can help me." This can be developed to the point where the focus is on the need for employee suggestions, and the supervisor can be asked how he thinks a process should be developed for it. In the end, a partnership can be formed, and you can work with the supervisor in solving his problem. First you have to gain his trust, and then you have to get him to identify the problem. Not easy, but if it were easy, anyone could do it. This method takes considerably longer but is much more likely to result in good long-term results. Culture is changed one manager at a time.
Going back to the story from beginning, my biggest successes - both in personal career growth and in organizational impact - has been when I turned our QA group (and it’s perception throughout the company) from policemen to change agents, coaches, leaders, consultants. I had my people make the first steps to reach out to the rest of the organization and to move from inspection to process control to problem solvers to process designers. Policing Quality is a lose/lose position for both the company and QA. While those measures may be required at times (tough love) it should be the action of last resort.
If the quality group doesn't lead quality improvement - who will?
Check out our fully customizable quality manual templates and procedures:
ISO 9001:2008 Quality Systems Manual and Procedures Templates Bundle
AS 9100 Quality Systems Manual Template
Please share your success stories, lessons learned, and ideas on the topic.
About the Author
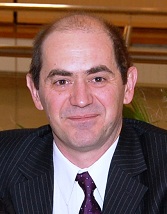
Steve holds a Master's degree in Mechanical Engineering and is ASQ Certified Manager of Quality/Organizational Excellence (ASQ CMQ), Certified Quality Engineer (ASQ CQE) and Certified Quality Auditor (ASQ CQA)
No comments:
Post a Comment